Contents
Automation, a term synonymous with efficiency and precision, has been a game-changer across industries, catapulting innovations and developments to unprecedented heights. In the realm of Electric Vehicle (EV) battery production, it’s a cornerstone, paving the path towards sustainability, a crucial attribute given the escalating climate concerns and resource constraints of our times. Automation within this sphere isn’t just a luxury; it’s a necessity, underpinning the very fabric of responsible and conscientious manufacturing.
The essence of sustainability in EV battery production lies in its ability to amalgamate environmental mindfulness with economic viability and social equity, ensuring a harmonious balance that caters to both present and future generations. This delicate equilibrium is pivotal, considering the heightened environmental awareness and the consequential push towards eco-friendly alternatives in the automotive sector.
Automation’s role in achieving sustainability in EV battery production is multifaceted. It helps in refining energy usage, optimizing resources, minimizing waste, and facilitating scalable solutions, aligning perfectly with the pressing need to incorporate sustainable practices. It becomes a harbinger of change, pushing the boundaries and transcending the limitations of traditional manufacturing processes.
Background of EV Battery Production
Overview of the EV battery production process:
Electric Vehicle (EV) batteries are at the heart of the burgeoning electric mobility revolution. These powerhouses are manufactured through a series of meticulously calibrated processes, including electrode preparation, cell assembly, formation, and aging. Each phase is critical, ensuring the optimal performance, safety, and longevity of the battery, and necessitates a high degree of precision and quality control.
Importance of sustainability in battery production:
With the expanding footprint of EVs globally, the production of their batteries is surging, intensifying the pressure on the associated resources and ecosystems. Sustainability in this context is not a mere token; it’s an imperative, dictating the judicious use of materials, energy-efficient processes, and minimized waste generation. It addresses the ecological impact, shaping the production practices to be harmonious with the environmental well-being and societal needs, fulfilling the triple bottom line of people, planet, and profit.
Challenges in maintaining sustainability in traditional production methods:
Traditional methods of battery production are often riddled with challenges, particularly when evaluated through the lens of sustainability. The high energy consumption, substantial waste generation, and extensive manual interventions not only inflate the operational costs but also pose significant environmental repercussions. The manual handling can also introduce inconsistencies, impacting the quality and reliability of the batteries, thus accentuating the urgency for more sustainable and efficient alternatives.
This is where automation emerges as the beacon of hope, offering solutions that are not only sustainable but also economically viable and socially equitable. By integrating automation, the production processes can be streamlined and optimized, addressing the inherent inefficiencies and inconsistencies of manual methods and ensuring the conformity to stringent quality standards.
The backdrop of EV battery production sets the stage for a detailed exploration of how automation intersects with sustainability. It provides a context to understand the transformative impact of automation technologies in mitigating the challenges and maximizing the potential for sustainable practices within the EV battery production ecosystem.
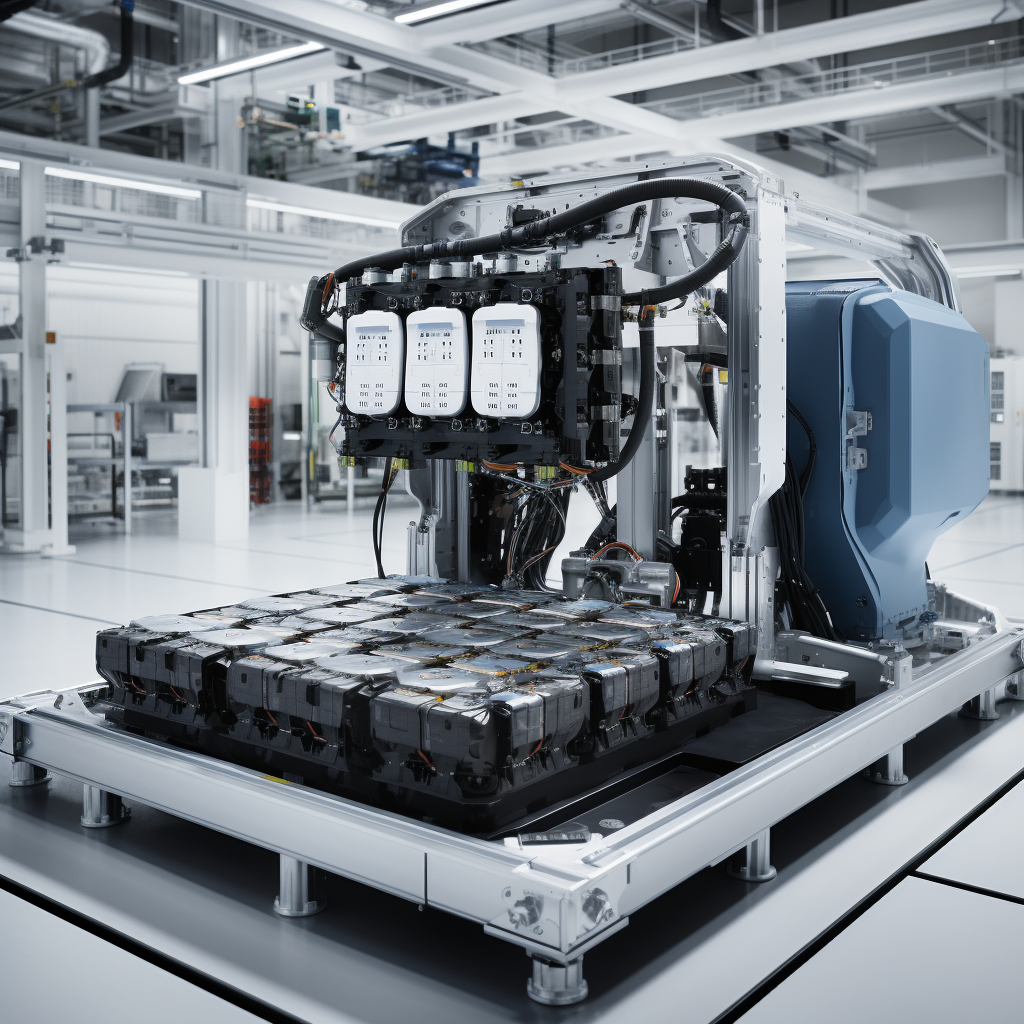
Impact of Automation on Sustainability
Energy Efficiency:
Automation has a transformative impact on the energy efficiency of EV battery production processes. Automated systems are adept at optimizing energy consumption by adapting operations and minimizing wastages, which is pivotal in reducing the overall carbon footprint of the production cycle. For instance, advanced robotic systems can operate with precision, ensuring that every action is carried out with the utmost accuracy, thereby eliminating redundant energy usage common in manual operations.
Resource Optimization:
In addition to energy conservation, automation plays a crucial role in optimizing the utilization of resources. Automated processes employ advanced technologies such as machine learning and computer vision to monitor and control the usage of materials with pinpoint accuracy. This precision leads to a significant reduction in waste generation and ensures that the raw materials are utilized to their fullest potential, underlining the principle of resource efficiency that is fundamental to sustainability.
Scalability:
One of the pivotal advantages of automation is its inherent scalability. Automated production lines can be scaled up or down based on the demand, without a proportional increase in resource consumption or waste generation. This scalability ensures that the production can meet the market demands promptly while adhering to sustainable practices. It also enables manufacturers to adapt to the fluctuating market trends swiftly, maintaining a balance between supply and demand.

Enhanced Quality and Consistency:
Automated systems ensure that each battery produced adheres to the predefined quality standards consistently. The precision and repeatability afforded by automation mitigate the risks of defects and inconsistencies, which, in turn, contribute to the longevity and reliability of the EV batteries. This enhancement in quality reduces the frequency of replacements and waste, aligning with the sustainability goals by promoting resource conservation and reducing environmental impact.
By impacting energy usage, resource consumption, scalability, and product quality, automation stands as a pillar supporting the sustainability objectives in EV battery production. It addresses the inherent challenges posed by traditional manufacturing methods and fosters the development of sustainable, reliable, and efficient production processes, essential for meeting the growing demand for EVs while safeguarding our environment and its resources.
Case Studies
Case Study 1: Tesla’s Gigafactory
Tesla, a frontrunner in the EV market, has been instrumental in integrating automation to achieve sustainability in EV battery production. The company’s Gigafactory in Nevada employs a plethora of automated processes aimed at optimizing energy consumption and minimizing waste. Tesla’s relentless pursuit of efficiency has led to a 70% reduction in water usage per kWh of battery capacity and has optimized energy consumption by employing heat recovery systems and natural lighting within the facility.
Case Study 2: LG Chem
LG Chem, another significant player in the EV battery domain, has implemented advanced automation technologies at its facilities, focusing on sustainable production methods. By utilizing machine learning algorithms and robotics, LG Chem has enhanced precision in material usage and improved energy efficiency, thereby reducing the environmental impact of their battery production processes. The company’s innovations have led to the development of batteries with higher energy density, contributing to the overall sustainability by extending the life-cycle of the batteries.
Case Study 3: CATL
Contemporary Amperex Technology Co. Limited (CATL), a global leader in manufacturing EV batteries, has integrated automation within its production lines to augment sustainability. The company utilizes automated assembly lines to ensure consistency and precision, which significantly reduces waste and optimizes resource usage. CATL’s initiatives in automation have streamlined its production processes, resulting in a considerable reduction in energy consumption and carbon emissions, aligning its operations with sustainability objectives.
Case Study 4: Panasonic
Panasonic, with its longstanding history in battery production, has incorporated automation to enhance sustainability within its production lines. The company’s focus on automation has resulted in significant advancements in energy efficiency and resource optimization. Panasonic’s commitment to sustainability is evident through its initiatives to minimize waste and improve recyclability of materials, thereby contributing to the development of eco-friendly EV batteries.
These case studies exemplify how leading companies are leveraging automation to address sustainability challenges in EV battery production. The implementations range from optimizing resource usage to enhancing energy efficiency, providing insights into the transformative potential of automation in advancing sustainability within this sector. These real-world applications depict the various approaches and methodologies adopted to align battery production with ecological conservation and sustainable development, offering a glimpse into the future possibilities and developments in this realm.

Benefits and Challenges of Automation in EV Battery Production
Benefits:
- Enhanced Productivity: Automation significantly boosts productivity by streamlining processes and eliminating unnecessary manual interventions. It enables the production lines to operate at optimal efficiency, increasing the overall output and allowing manufacturers to meet the rising demand for EV batteries effectively.
- Optimized Resource Utilization: The precision afforded by automation minimizes wastage of materials and ensures optimal utilization of resources, contributing to the sustainability goals by reducing the environmental footprint of the production processes.
- Improved Quality and Reliability: Automated systems maintain a consistent quality of production, reducing the likelihood of defects and enhancing the reliability and longevity of the EV batteries, which in turn, decreases the frequency of replacements and waste generation.
- Cost-Efficiency: While the initial investment in automation technologies may be substantial, the long-term benefits, including reduced operational costs, optimized resource usage, and increased productivity, render automation a cost-effective solution in the realm of EV battery production.
Challenges:
- High Initial Investment: The implementation of automation technologies requires a substantial initial investment, which can be a significant barrier for smaller manufacturers aiming to adopt sustainable production practices.
- Complexity in Implementation: The integration of automation in production lines can be complex, necessitating specialized knowledge and expertise to ensure seamless operation and alignment with sustainability goals.
- Dependence on Technology: The reliance on automated systems can pose risks in the event of technical failures or malfunctions, potentially disrupting the production processes and impacting the sustainability of operations.
- Job Displacement: The transition from manual to automated processes can lead to job displacement and require reskilling and upskilling of the workforce to adapt to the evolving industrial landscape.
In conclusion, while the benefits of automation in enhancing sustainability in EV battery production are manifold, the challenges necessitate thoughtful consideration and strategic planning. The amalgamation of automated processes and sustainable practices holds the potential to revolutionize the EV battery production landscape, balancing ecological conservation with economic viability and social equity. Addressing the challenges and leveraging the benefits of automation are pivotal in navigating the path towards a sustainable future in EV battery production.
Future Outlook and Conclusion
Future Outlook:
The integration of automation in the EV battery production realm is set to witness prolific advancements and refinements in the coming years. The continuous pursuit of sustainable practices will drive innovations aimed at optimizing resource utilization, minimizing environmental impact, and enhancing the overall efficiency of the production processes.
- Advanced Robotics and AI: The future will see the convergence of advanced robotics and Artificial Intelligence to create smarter, more efficient, and adaptable production systems. These systems will be capable of learning and evolving, ensuring continual improvements in sustainability measures.
- Sustainability-Centric Innovations: With sustainability at the forefront, innovations will be primarily directed towards developing technologies and methodologies that not only enhance production efficiency but also emphasize ecological conservation and responsible resource management.
- Holistic Sustainability Approach: The focus will shift towards a holistic approach to sustainability, encompassing every aspect of the production cycle. This approach will address environmental, social, and economic dimensions, aiming to achieve a balanced and inclusive development in EV battery production.
Conclusion:
Automation stands as a transformative force in the EV battery production sector, merging efficiency with sustainability. It addresses the critical need for ecological conservation, optimal resource utilization, and energy efficiency, all while catering to the escalating demand for electric vehicles.
The journey of integrating automation and sustainability is marked by challenges, but the benefits outweigh the obstacles. Leading companies like Tesla, LG Chem, CATL, and Panasonic are pioneering this convergence, showcasing the tangible impacts and the potential it holds. The future promises a surge in innovations, centering around sustainability, advanced technologies, and holistic approaches, offering a vision of a harmonious and balanced coexistence of industrial advancement and environmental conservation.
The evolution of automation in EV battery production is not merely a technological transition; it is a paradigm shift towards a sustainable and equitable future. It underscores the symbiotic relationship between technology and sustainability, elucidating a pathway that intertwines ecological responsibility with industrial progress, and fortifies the foundations for a green and inclusive future in electric vehicle technology.